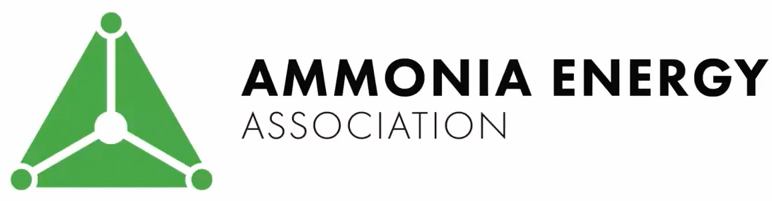
By
Kevin Rouwenhorst on November 11, 2022
Production technology updates: from
mega-scale to distributed ammonia
Historically ammonia plants have increased
in size to benefit from
economies of scale. The largest current single train ammonia plant
has an ammonia production capacity of
3,670 metric tonnes per day, and is operated by SAFCO in Saudi
Arabia. Recently, KBR launched its Ammonia 10,000 technology for
newbuild ammonia plants,
tripling the available single train ammonia plant capacity to
10,000 metric tonnes per day. In our latest Technology Insights
article, we explore the other pieces of the puzzle required for
mega-scale ammonia, as well as some updates from the other end of the
spectrum: distributed, small-scale ammonia synthesis.
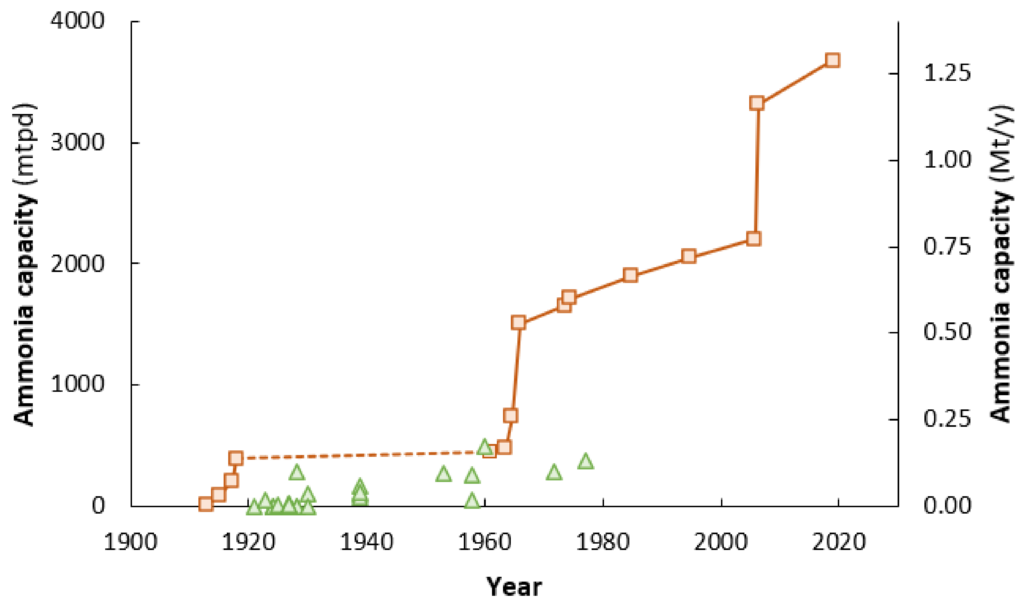
Ammonia production (individual unit
capacities) over the last century, both fossil-based ammonia
production (brown squares), and renewable ammonia production (green
triangles). From Rouwenhorst et al., “1921–2021:
A Century of Renewable Ammonia Synthesis”, Sustain. Chem.
(April 2022).
Scale-up of ammonia plants
Historically, scale-up has been
facilitated by technological developments, such as the introduction of
centrifugal compressors in the 1960s. Global demand for ammonia
and fertilizers subsequently increased, confirming that further
scale-up was economic. A benefit of scaling up the single train
ammonia synthesis capacity is the lower relative capital expenditure (CAPEX)
for larger ammonia plants. For example, a size increase by a factor of
five typically only results in a CAPEX three times that of the
original value.
As mentioned above, the largest
operational single train ammonia plant has a capacity of 3,670 metric
tonnes per day (ThyssenKrupp Uhde design), equivalent to about 1.3
megatonnes per annum. Various licensors have announced technology for
larger capacities, such as
Casale’s A6000 technology (5,000 – 6,000 metric tonnes per day),
and
Topsoe’s SynCOR AmmoniaTM technology (4,000 – 6,000
metric tonnes per day). KBR’s new technology triples the largest
operational production capacity, equivalent to up to 3.5 megatonnes of
ammonia per annum.
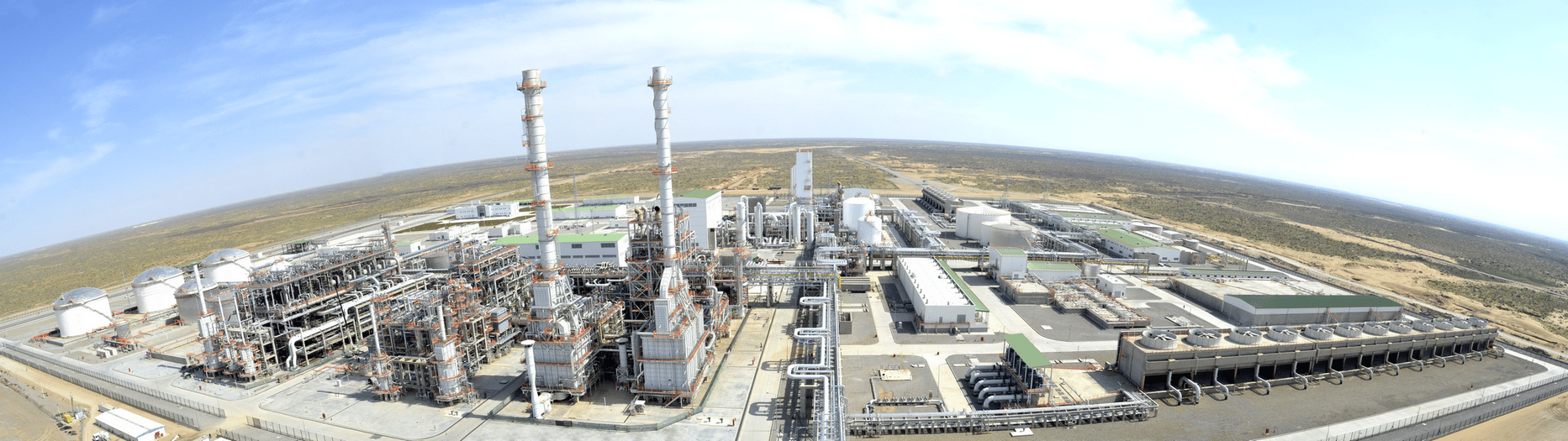
Topsoe’s TIGAS plant in
Turkmenistan, the world’s largest operating, ATR-based hydrogen
production facility. Source: Topsoe.
Scaling hydrogen production
Ammonia synthesis also requires scale-up
of hydrogen production. Current, fossil-based hydrogen production
relies on either steam methane reforming (SMR), or autothermal
reforming (ATR) technologies.
ATR benefits more from scale-up than
steam methane reforming, and CO2 capture has a lower cost
when applied to ATR. Announced ammonia production technologies with a
capacity of 4,000 metric tonnes per day and above are exclusively
based on hydrogen in an autothermal reformer. Available technology for
autothermal reforming would theoretically allow for production of up
to 7,000 metric tonnes of ammonia per day. The
largest operational ATR-based hydrogen production plant – if
utilized for ammonia production – would produce 3,700 metric tonnes
per day ammonia equivalent.
Scaling electrolysis & air
separation
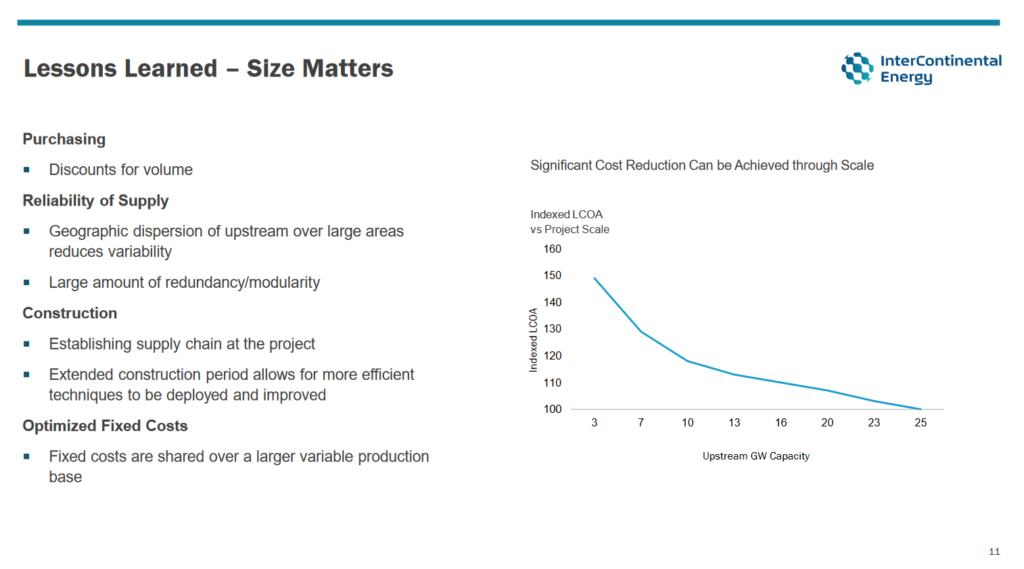
Lessons learned from GW-scale
ammonia project development. From Alex Tancock,
Green Ammonia at Oil & Gas Scale (Nov 2020).
Renewable ammonia requires separate
hydrogen production and nitrogen production. Hydrogen is produced via
water splitting in electrolyzers, whereas nitrogen is purified from
air via cryogenic distillation in an air separation unit (ASU).
Nitrogen purification via ASU benefits
even more from economies of scale than ammonia synthesis loops. A
tenfold capacity increase for nitrogen purification only results in a
threefold increase of the capital expenditure. Moreover, nitrogen
purification is already at the required scale. The
largest single ASU was recently announced in China, where Air
Liquide will invest around $118 million for its construction. This
plant produces enough purified nitrogen to produce 14,925 metric
tonnes of ammonia per day.
Hydrogen production from electrolysis is
modular, just like upstream solar and wind resources. This means that
electrolysis systems are not necessarily benefiting from economies of
scale. However, project developers for large-scale electrolysis
projects may
benefit from purchasing discounts, shared utilities and personnel,
as well as renewable electricity with a higher overall load factor
with reduced variability.
IEA estimates that the global installed
electrolyzer capacity will be 1.4 GW by the end of 2022. According to
size estimates of Del Pozo et al., a 10,000 metric tonnes per day
ammonia plant would require about 5.4 – 7.5 GW of installed
electrolyzers. It’s no secret that electrolyzer manufacturing &
deployment will need to scale up, and drastically.
Within this decade, the first million
tonnes per annum renewable ammonia plants are expected. On the longer
term, renewable ammonia “Supergiant” projects have progressed, most
notably the
Asian Renewable Energy Hub,
InterContinental Energy’s extended project portfolio and
CWP Global’s projects in Mauritania and Morocco.
From Supergiants to small-scale
At the other end of the scale to the
Supergiants, distributed ammonia production systems may prove an
essential tool to improve energy & food security, reduce costs for
agricultural producers and help deploy ammonia energy solutions in
everyday settings. This may be especially relevant for isolated
locations without pre-existing ammonia and fertilizer infrastructure
nearby, as fertilizer availability and cost are key issues in these
locations.
Starfire Energy have just announced
completion of a successful,
$24 million Series B funding round. Funds will aid the
commercialization of their
Rapid Ramp© ammonia production system (100 kg per day), which
Starfire says requires no hydrogen or energy storage backup to
operate. Air, water and renewable energy are the only inputs required.
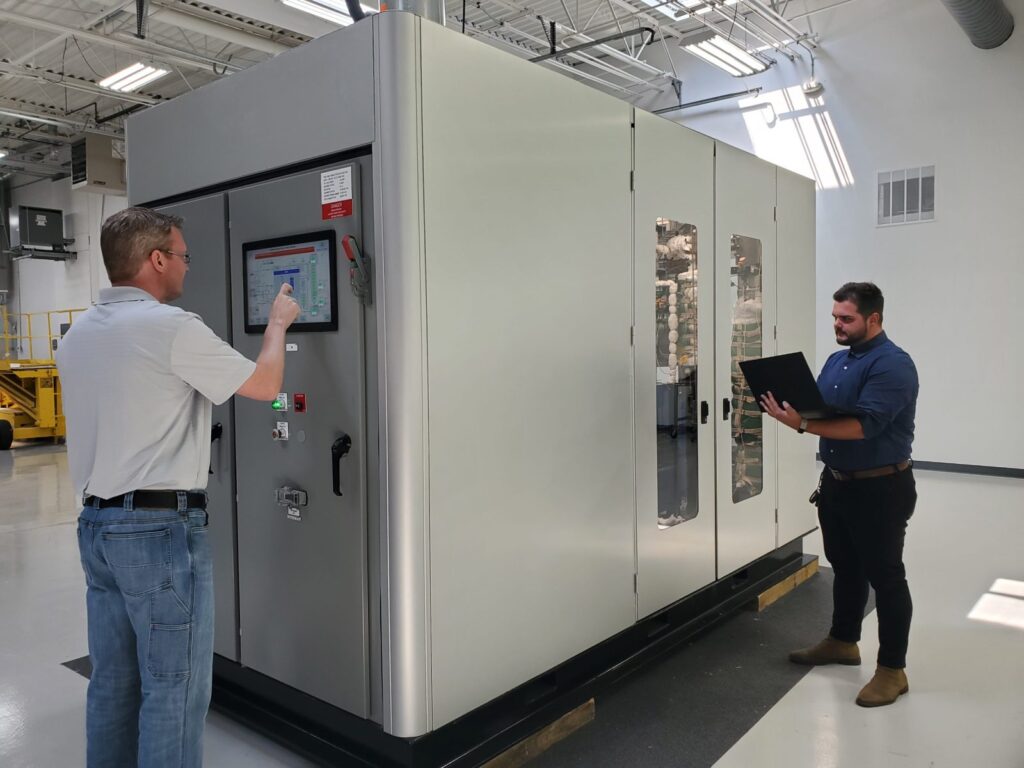
A demonstration unit of AmmPower’s
Independent Ammonia Making Machine™ (IAMM™). Source: AmmPower
Corportaion.
AmmPower announced successful testing of
their
Independent Ammonia Making Machine™ (IAMM™) in early November. The
demonstration unit produces 50 kg per day of ammonia, which will be
scaled to 4 metric tonnes per day for the commercially-available IAMM™
units. Assembly of the first units was due to begin last month in
Michigan, USA.
And FuelPositive are in the final stages
of validating a demonstration unit for its containerized, point-of-use
ammonia production system. Once the tick of approval is given, the
system will be
installed and commissioned on an 11,000 acre crop farm in
Manitoba, Canada for extensive field testing. The 300 kg per day
system is set to be “farm-ready” by the end of the year.
Green Play Ammonia™, Yielder® NFuel Energy.
Spokane, Washington. 99212
www.exactrix.com
509 995 1879 cell, Pacific.
exactrix@exactrix.com
|