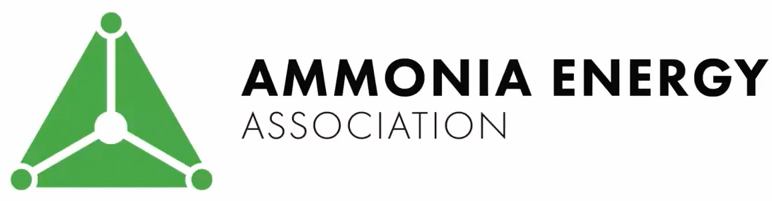
SOEC
electroyzers, Haldor Topsoe.
For opex, which is dominated by energy costs in any ammonia
technology, the SOEC-HB is estimated to produce green ammonia with a
specific energy consumption of about 7.2 MWh per ton, which is 26 GJ
per ton. In
other words, its green ammonia plant could be more energy efficient
than today’s best state-of-the-art natural gas-fed ammonia plant,
which consumes around 28 GJ per ton.'
It
should be noted that these figures are for a small demo plant.
Topsoe Haldor, who as the article noted are experts in ammonia
production with 60 plants up and running, are confident enough already
to scale to full industrial size.
I
don't really understand how the Haber-Bosch units tie in with the
electrolytic production, perhaps those who are more technically
knowledgeable than I, which is a large part of the population, would
elucidate?
Haldor Topsoe has greatly improved the
near-term prospects for green ammonia by announcing a demonstration of
its next-generation ammonia synthesis plant. This new technology uses
a solid oxide electrolysis cell to make synthesis gas (hydrogen and
nitrogen), which feeds Haldor Topsoe’s existing technology: the Haber-Bosch
plant. The product is ammonia, made from air, water, and renewable
electricity.
The “SOC4NH3” project was recently
awarded funds from the Danish Energy Agency, allowing Haldor Topsoe to
demonstrate the system with its academic partners, and to deliver a
feasibility study for a small industrial-scale green ammonia pilot
plant, which it hopes to build by 2025. There are two dimensions to
this technology that make it so important: its credibility and its
efficiency.
First, the technology owner: Haldor
Topsoe is a highly respected technology development company, and it
commands a global market-leading position in the ammonia industry (it
has built 60 ammonia plants since 2000 and currently services 248
ammonia catalyst charges around the world). Haldor Topsoe’s status
makes it credible when it claims, as it does in
recent presentations, that its new technology could be
commercially available by 2030.
Second, the technology: Haldor Topsoe’s
solid oxide electrolysis cell (SOEC) ammonia plant represents an
optimized integration of electrolyzer and Haber-Bosch (HB) units. It
has the potential to reduce both capex and opex, relative to other
electrolyzer technologies but also relative to conventional ammonia
plants using natural gas. The system has been designed to reduce capex
by eliminating the need for an air separation unit (ASU). This is nice
for the prospects of large-scale green ammonia but, combined with the
scalability of electrolyzers, it significantly improves the economics
of small-scale ammonia production (at small scales, the ASU becomes
very expensive). For opex, which is dominated by energy costs in any
ammonia technology, the SOEC-HB is estimated to produce green ammonia
with a specific energy consumption of about 7.2 MWh per ton, which is
26 GJ per ton. In other words, its green ammonia plant could be more
energy efficient than today’s best state-of-the-art natural gas-fed
ammonia plant, which consumes around 28 GJ per ton.
SOC4NH3 project funding
SOC4NH3 is one of 46 projects that were
awarded grants at the end of 2018 totaling DKK 234 million (USD $36
million) by the Danish Energy Agency, through its Energy Technology
Development and Demonstration Program (EUDP). The EUDP funding is
intended to help local companies to commercialize sustainable
technologies, which can then be exported.
“[EUDP] contributes to knowledge about
the green projects of the future, and it especially contributes to
increasing export of energy technology solutions. For each unit of
allocated state subsidy, we increase export[s] two fold …
We need to research and develop new
solutions that can contribute to tackling the major issue of climate
change the world is facing. If we are to be a front runner, it is
important to always focus on the newest technologies, and these
grants contribute to that end.”
Danish Minister of Energy, Utilities and Climate, Lars Christian
Lilleholt, quoted in
Funding for robots and climate-friendly ammonia to accelerate green
energy, Energy Watch, 12/20/2018
SOC4NH3 has a total budget of DKK 26.8
million (about USD $4 million), of which the EUDP is contributing DKK
15.9 million. The project began in January 2019 and runs through April
2022.
The SOEC will be demonstrated alongside
another new Haldor Topsoe technology: a solid oxide fuel cell (SOFC)
that generates combined heat and power using ammonia as a fuel. In
full, there are four elements to the SOC4NH3 project:
- Demonstration of green ammonia
production from renewable energy, air, and water, using a 50 kW
solid oxide electrolysis cell (SOEC), at the
University of Aarhus in Foulum.
- Demonstration of combined heat and
power generation from ammonia fuel, using a 1.5 kW single stack
solid oxide fuel cell (SOFC), at DTU (Danmarks Tekniske Universitet)
Department of Energy Conversion and Storage.
- Techno-economic and socio-economic
studies on the production of green ammonia and use of ammonia as an
energy vector in a decarbonized economy.
- Engineering design and site-specific
feasibility study for an industrial-scale (1-2 metric ton per day)
green ammonia pilot plant, using Haldor Topsoe’s all-electric SOEC
ammonia technology.
A new research project, SOC4NH3 (Solid
Oxide Cell based production and use of ammonia) with a number of
strong partners will over the next years develop and demonstrate the
technology and thereby bring it a big step closer a commercial
breakthrough.
“We expect that ammonia can be used for
transportation and efficient storage of energy. The greatest
advantage of ammonia is that it has a high energy density which
makes it an effective fuel and energy storage option – and it can
thereby solve some of the most important challenges of creating a
sustainable energy system of the future,” says project leader,
Senior Principal Scientist John Bøgild Hansen, Haldor Topsoe A/S.
Haldor Topsoe announcement,
Ammonia can become the CO2-free fuel of the future, 02/21/2019
Haldor Topsoe’s commercial partners for
the techno-economic and socio-economic studies, contributing
perspectives from across the entire energy value chain, include
Energinet, the Danish electricity and natural gas distributor; Vestas,
a global market leader in wind turbine manufacturing; Equinor,
Norway’s national oil company; and Ørsted Wind Power (“We’ve built
more offshore wind farms than any other developer in the world
and we’ve only just begun“).
Haldor Topsoe’s SOEC
energy efficiency
Perhaps the most important aspect of
Haldor Topsoe’s SOEC-HB technology, beyond the fact that it can be
carbon-free, is its promise of higher energy efficiency.
In conventional plants today, ammonia is
made by combining hydrogen, produced from coal or natural gas or
another fossil fuel, with nitrogen, produced by an air separation unit
(ASU). Fossil hydrocarbons aren’t the only viable source of hydrogen
but, in most places, they are the cheapest. I’ve previously written
about how today’s natural gas-fed
Haber-Bosch plant is almost perfectly energy efficient, due to
decades of incremental innovation co-optimizing the steam methane
reformation (SMR) units, which produce hydrogen from natural gas, and
the HB units.
Since the start of the 20th Century,
however, ammonia plants around the world have used electrolyzers to
produce hydrogen from water, making industrial quantities of
carbon-free “green” ammonia. Due to economics, only a couple of these
plants still operate today. This technology always uses alkaline
electrolysis cells (AEC) to produce the hydrogen that is fed to the HB
unit. AEC is a mature technology but, unlike SMR, it did not evolve
alongside HB; it has not been integrated and co-optimized over decades
into the design and engineering of an ammonia plant.
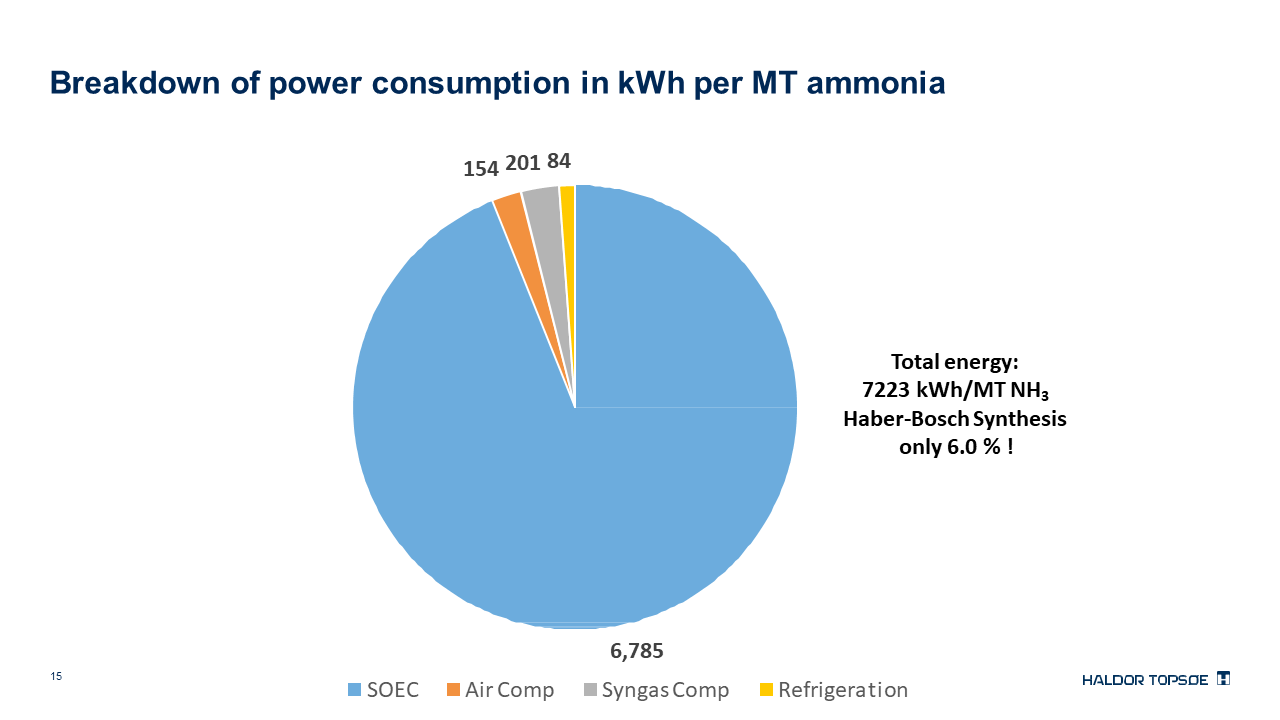
John Bøgild Hansen, NH3
Fuel Conference presentation,
Solid Oxide Cell Enabled Ammonia Synthesis and Ammonia Based Power
Production, November 2017.
The latest AEC ammonia technology will be
demonstrated in a
pilot plant in South Australia, with an estimated energy
consumption of 10 MWh per ton of ammonia. That is roughly equivalent
to 36 GJ per ton, which is the ammonia industry’s current average net
energy efficiency (according to the
IFA Benchmark). This is respectable performance but less energy
efficient than today’s best available (fossil) technology (roughly 28
GJ per ton for a state-of-the-art, world-scale SMR-HB plant).
Haldor Topsoe’s new SOEC-HB, on the other
hand, is estimated to produce ammonia with an energy consumption of
about 7.2 MWh per ton. This is roughly 26 GJ and is better than
today’s best available technology.
Of this 7.2 MWh per ton, 94% of the
energy is consumed by the SOEC in the production of synthesis gas
(hydrogen and nitrogen) and only 6% is used by the HB unit for ammonia
synthesis.
Haldor Topsoe’s SOEC
cost efficiency
Exactly like AEC-HB, an SOEC could be
used to produce hydrogen, alongside an ASU to produce nitrogen, in
order to feed the HB unit. This green ammonia plant would represent a
conventional use of an electrolyzer, but it would be an unintegrated,
unoptimized technology. Compared to the AEC, the SOEC exhibits a
fundamentally different chemistry, with perhaps greater potential for
optimization with the HB unit. Haldor Topsoe has focused on this
potential.
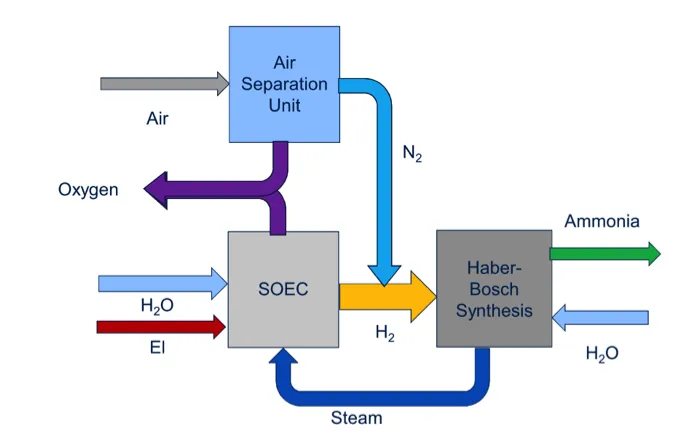
Process flow diagram to show solid oxide
electrolysis cell and air separation unit feeding Haber-Bosch unit.
Source: Haldor Topsoe.
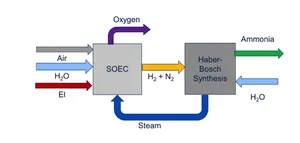
The AEC splits water by transporting
hydroxide ions (OH–) across a membrane, whereas the SOEC
transfers oxide ions (O2-) across its membrane. It is the
oxygen separating aspect of this chemistry that allows Haldor Topsoe
to make a major cost-saving change in its design of a green ammonia
plant: the elimination of the ASU. In Haldor Topsoe’s integrated
technology, the SOEC produces both the hydrogen and the nitrogen
required by the HB unit.
The nitrogen is producw-ed from the air
input simply by burning some of the hydrogen that was made by the
electrolyzer, which removes oxygen from the air and generates steam.
This means that the electrolyzer must produce more hydrogen than the
HB unit alone requires, implying a hit to the system’s energy
efficiency. However, another aspect of the SOEC that differentiates it
from the AEC is its ability to consume power in the form of either
electricity or heat. Therefore, the steam generated by burning
hydrogen can be almost completely recycled within the system,
providing both water input and heat energy to the electrolyzer, and
thus allowing the system to operate at a lower voltage. In this way,
the high energy efficiency of the SOEC can be almost completely
maintained while eliminating the ASU from the system.
This energetic trade-off – swapping heat
for electricity – has an economic impact: the capital savings achieved
by eliminating the ASU from the system are earned by investing in an
expanded SOEC stack area. The techno-economic study coming out of the
SOC4NH3 project will aim to identify the project specifications and
market conditions to optimize this trade-off.
You can also read the
full article at AmmoniaIndustry.com.
Green Play Ammonia™, Yielder® NFuel Energy.
Spokane, Washington. 99212
www.exactrix.com
509 995 1879 cell, Pacific.
exactrix@exactrix.com
|