Engineers from the SSAB steel-making
company have unveiled the world’s first piece of steel cast
without burning any coal or fossil fuel. Instead, they used
hydrogen to power the process.
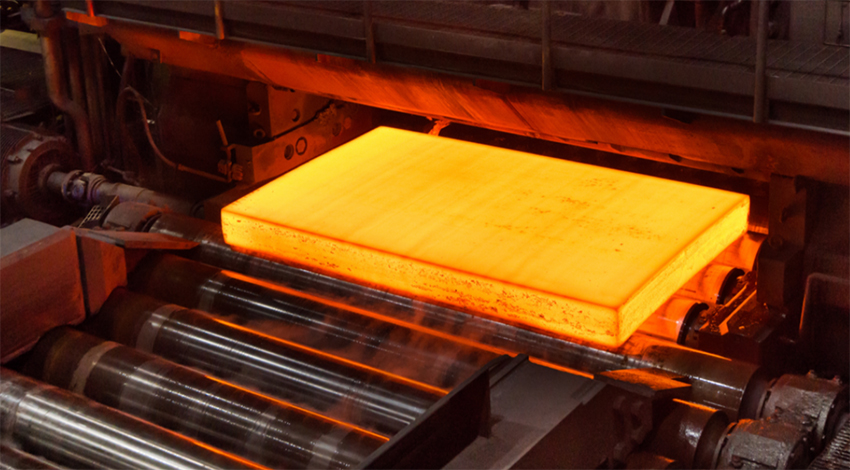
Metalworking and coal burning have been
entwined for as long as humanity has been using metals.
Coal is a very good source of energy, providing the heat necessary
to refine and process most metals. But it is also a source of carbon,
a critical chemical in the production of steel, and the compound that
allows us to turn metal ores (usually oxides) into actual metals (by
leaching out the oxygen).
For most of our history, this wasn’t that
much of an issue. Coal smoke is definitely not healthy for you or
anyone living near the smeltery or ye olde blacksmith, but overall
production of metals was limited in scope — so the environment could
absorb and process its emissions.
Today, however, the sheer scale at which
we produce metals means that this process has a real impact on the
health of the world around us. However, new technology could uncouple
the process from coal, and pave the way towards ‘green’ metals.
Engineers from the international, Sweden-based steel-making company
SSAB have showcased the process, which relies on hydrogen instead of
coal to produce the necessary temperatures.
“The first fossil-free steel in the
world is not only a breakthrough for SSAB, it represents proof that
it’s possible to make the transition and significantly reduce the
global carbon footprint of the steel industry,” said Martin
Lindqvist, SSAB’s president and CEO, for
CNBC.
The “hybrid process” used by SSAB uses
hydrogen as fuel to produce the required energy, instead of the
traditional approach of burning coal. This process, called HYBRIT
(Hydrogen Breakthrough Ironmaking Technology), uses electricity
produced through renewable means to produce hydrogen, which is in turn
burned to generate heat. Although there is burning involved, it
doesn’t produce any pollution — in fact, the only end product is
water.
HYBRIT can be used both for the
production of iron pellets — the main raw material used by steel
foundries — and in the carbon purification process, which is the step
that transforms iron into steel. The first piece of HYBRIT steel was
produced for the Volvo Group and is going to become a part of the
company’s fleet of trucks. A candleholder was also machined from this
steel as proof that its mechanical properties are the same as regular
steel produced by SSAB.
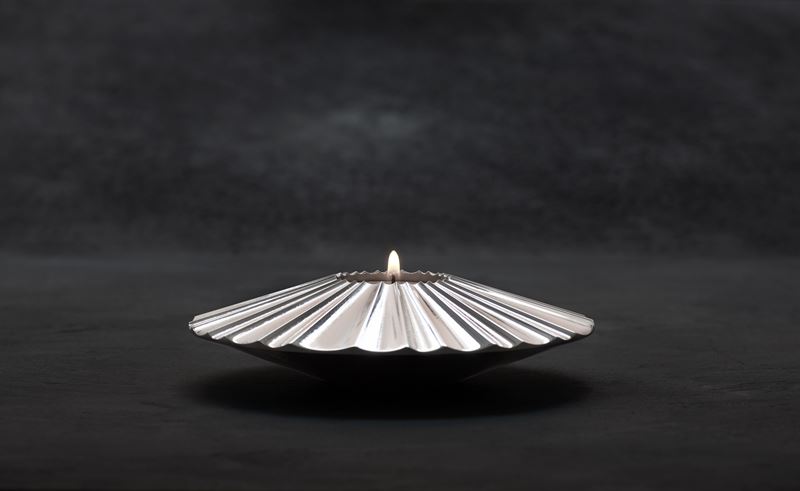
“The candle holder, with its softly pleated
rays beaming out from the candle, symbolizes the light at the end of
the tunnel. It is a symbol of hope. It truly is a piece of the
future,” says Lena Bergström, who designed the item.
The steel industry today accounts for
roughly 9% of global carbon dioxide emissions, and demand for (as well
as production of) steel is steadily increasing.
SSAB developed the process in the context
of a joint venture with the government-owned utility Vattenfall and
Swedish mining company LKAB. The steel was processed in a pilot plant
in the north of Sweden, and full-scale production capability is not
expected for another five years or so, according toReuters.
The slab of metal produced so far marks the culmination of
over 5 years of research and development of the HYBRIT process.
“The goal is to deliver
fossil-free steel to the market and demonstrate the technology on an
industrial scale as early as 2026,” a
statement form SSAB explained.
Green Play Ammonia™, Yielder® NFuel Energy.
Spokane, Washington. 99212
www.exactrix.com
509 995 1879 cell, Pacific.
exactrix@exactrix.com
|